White plastisol ink is available as thick opaque paste. Plastisol ink is made up of PVC resin (a white powder) and plasticizer (a thick, clear liquid). Plastisol ink will not dry, or cure, at normal temperatures. They must be exposed at a temperature around (143-166º C) to be properly cured. The stencil will not dry out after starting printing. White plastisol ink is best for getting a white solid uniform opaque print out for customer satisfaction. For getting a professional white print out without fibrillation, screen printer need to follow the following.
- Consistency of the ink : If the ink is stored for long period it becomes very thick. If so, we need to add a small amount of plastisol reducer. The ink and the reducer need to be mixed together thoroughly for some time using a paint mixing palette or electrical mixer so that the PVC resin + plasticizer + reducer get mixed evenly resulting in a more soft flexible butter like ink so that the printer is able to move and spread the ink freely over the screen and able to print it without much effort.
- Mesh count : As more ink need to pass through the minute holes of the stencil mesh count of the cloth (bolting cloth) need to be 100. If we use mesh above 100 the amount of ink deposit will be less. Tension of the cloth need to be high as it affect the quality of print out.
- ½ Coating of emulsion : As thick layer of white ink need to be deposited over the black fabric, the two layers of coating needed on the outer side and one layer is enough on the inner squeegee side. After coating the screen need to be kept horizontally for air drying inside the drying rack.
- Printing : Well dried exposed stencil is placed over the platen with sufficient off contact. Adhesive spray is applied over the platen so that the tee shirt will get fixed over the platen without any folding. Before printing ink is pasted all over the stencil without much pressure. Single impression is done using a 65 – 70 Dura meter squeegee. Thin layer of white ink is deposited over the fabric. By using heat gun or flash unit partial curing is done. This is followed by the second and third impression if needed. Take the tee shirt from the platen and do the final curing. The temperature 143-166º C and timing need to be correct. During curing PVC resin and plasticizer react together result in the formation of a thin white plastic like layer into the fabric. Over curing and under curing undesirable. Wash test and stretch test is done finally.
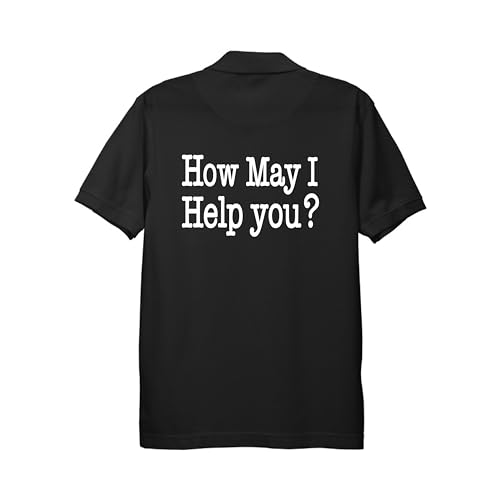